Share
Pin
Tweet
Send
Share
Send
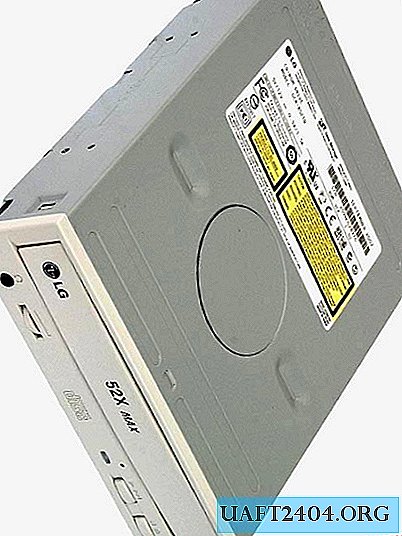
The device must be completely disassembled. For further work you will need:
- plastic base, with an engine and gearbox extension mechanism,
- movable tray,
- Front panel board with volume control.
For reciprocating movement of the tray, we use a crank mechanism. The gears of the gearbox must be carefully removed. The gear gear meshing with the gear rack of the tray requires a little refinement. From the gear rims on the top and bottom of the gear you need to remove two teeth with a mock knife, freeing up space for installing the crank axis. The axis is a threaded sleeve and is mounted on the upper side of the gear with a short screw.


The modified gear should be tried on to make sure that there are no obstacles to free rotation. The screw head, along the trajectory of its movement, can touch the base. This difficulty is eliminated with a breadboard knife, the base plastic is removed at the points of contact with the screw head. Mobile tray, finalized according to plan. Using a hacksaw blade, the rack is removed.

In the place where the crank is located, a hole is made in the tray (in my case, about 20 by 40 mm.), In order to simplify the assembly and avoid touching the axis of the crank over the bottom surface of the tray.
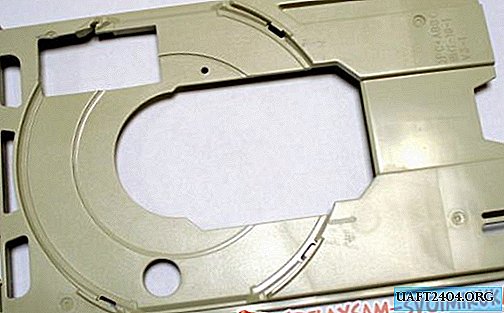
Now you can assemble the gearbox and check the mobility of the parts.

To transfer movement to the tray, you will need to make a connecting rod.
I made a connecting rod from a thick paper clip and two electrical terminals, with a hole with a diameter of 3 mm. Workpieces are connected by soldering.

The connecting rod is mounted movably on the tray, using the M3 screw and a nut with a lock nut. On the axis of the crank, screw M3 (so long as to abut the screw securing the threaded sleeve, while maintaining the mobility of the connecting rod).
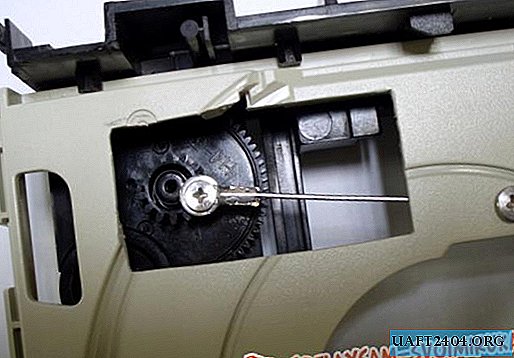
To smoothly change the oscillation frequency of the tray, I made a regulator to control the drive motor.

The circuit is a simple stabilizer, the voltage is adjustable from 0 to 6.5 volts.
Stabilizer parts are mounted mounted on the front panel board.
Remove all components except the variable resistor from the board.
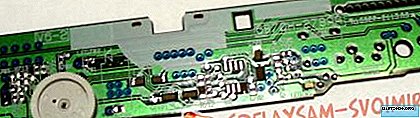
Traces of the circuit board through which undesired connections may form can be torn with a scalpel. Two sections of the variable resistor are connected in parallel. The current flowing through the motor is not large, additional measures for cooling the regulator transistors are not required. For clarity, I depicted the wiring diagram of the controller with all the connections.

Soldered joints at the terminals of the transistors are insulated with a heat shrink tube. Transistors are mounted on the back of the board.
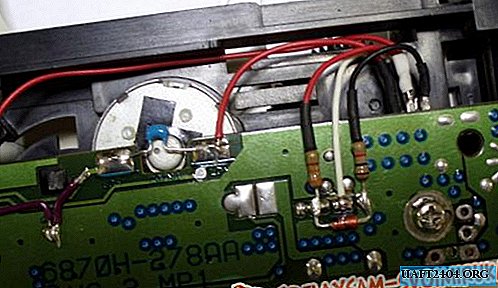
A power supply with a constant voltage of 7.5 to 12 volts can be "borrowed" from a modem, router, wireless access point, etc.
I used the power supply from the DECT of a Panasonic phone (for most of the time it works for its intended purpose).
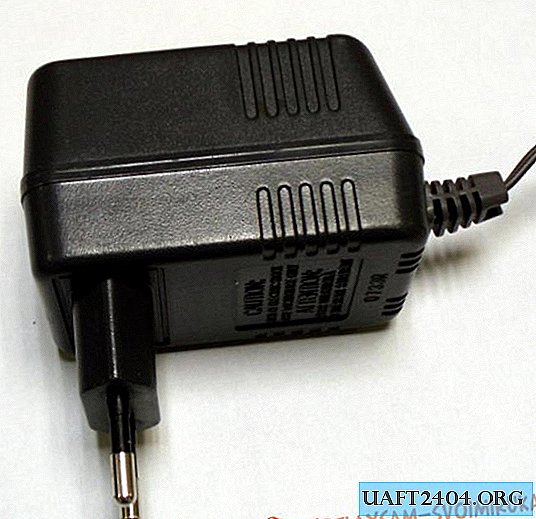
Of course, that to the connector on the power supply, you need to choose the appropriate connector for installation on the board and connect it correctly.
On the whole, the shaker turned out to be unpretentious and useful in all respects.

It is convenient to use plastic ice cream trays as a container for etching boards. The volume of solution is usually 100 - 150 ml, the etching time of printed circuit boards is significantly reduced (even with weak and old solutions). Due to the uniformity of the etching and the shorter residence time of the board in the solution, it is possible to avoid characteristic defects ("ghosting" and "grating").
Share
Pin
Tweet
Send
Share
Send